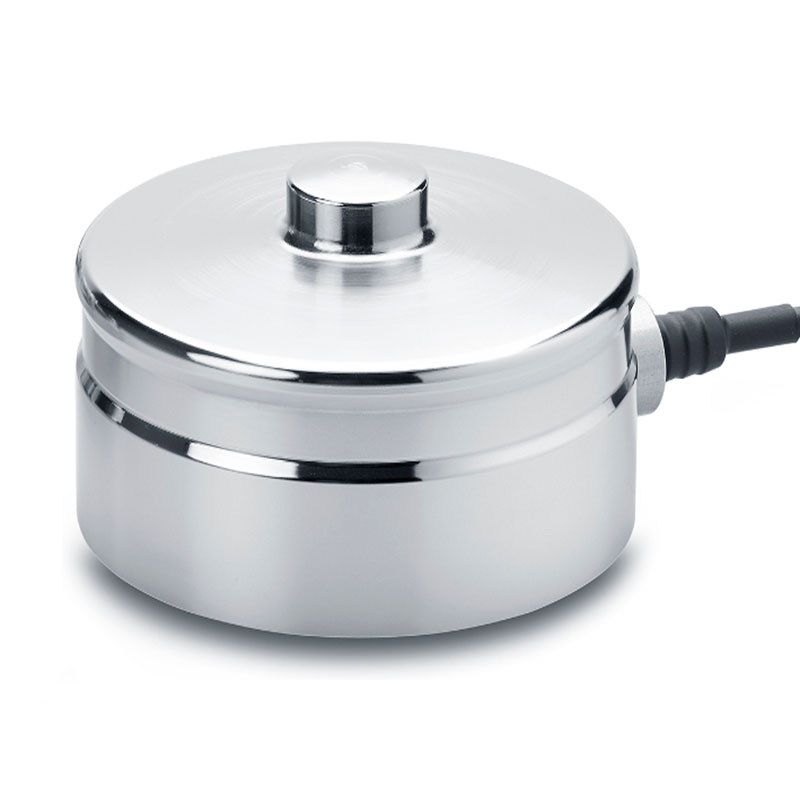
Weighing sensor
brief introduction:The load cell is actually a kind of device which transforms the mass signal into measurable electrical signal output. The actual working environment of the sensor should be considered before using the sensor, which is very important for the......
The load cell is actually a kind of device which transforms the mass signal into measurable electrical signal output. The actual working environment of the sensor should be considered before using the sensor, which is very important for the correct selection of the weighing sensor. It is related to the normal operation of the sensor, its safety and service life, and even the reliability and safety of the whole weighing instrument. There are qualitative differences between the old and the new national standards in the basic concepts and evaluation methods of the main technical indicators of the load cell. There are mainly S-type, cantilever type, spoke type, plate ring type, membrane box type, bridge type, cylinder type and other types.
According to the conversion method, the load cell can be divided into eight types: photoelectric type, hydraulic type, electromagnetic force type, capacitance type, magnetic pole change type, vibration type, gyroscope ceremony type, resistance strain type, etc.
Photoelectric load cell
It includes grating type and code disk type.
Grating sensor uses moire fringe formed by grating to convert angular displacement into photoelectric signal. There are two gratings, one is a fixed grating, the other is a moving grating mounted on the dial shaft. The object on the load-bearing platform makes the dial axis rotate through the force transfer lever system, which drives the moving grating to rotate, and makes the moire fringe move with it. The number of moire fringes can be calculated and the rotation angle of grating can be measured by using photocell, conversion circuit and display instrument, so as to determine and read out the mass of the measured object.
The code plate (symbol board) of the encoder type sensor is a transparent glass which is installed on the dial shaft with black and white code coded according to a certain coding method. When the measured object on the load-bearing platform rotates the dial shaft through the force transfer lever, the code plate also turns a certain angle. The photocell will receive the optical signal through the code disk and convert it into electrical signal. Then the circuit will carry out digital processing, and finally display the number representing the measured quality on the display. Photoelectric sensor used to be mainly used in mechanical and electrical scales.
Hydraulic load cell
Under the action of gravity P, the pressure of hydraulic oil increases, and the degree of increase is proportional to P. The mass of the measured object can be determined by measuring the increase value of the pressure. The structure of the hydraulic sensor is simple and firm, and the measurement range is large, but the accuracy generally does not exceed 1 / 100.
Capacitive load cell
It works by using the positive proportional relationship between the oscillation frequency f of the capacitor oscillation circuit and the plate spacing D (Fig. 6). There are two plates, one fixed and the other movable. When the load-bearing platform is loaded with the measured object, the leaf spring flexes, the distance between the two plates changes, and the oscillation frequency of the circuit also changes. The mass of the object on the bearing platform can be obtained by measuring the change of frequency. The capacitance sensor has the advantages of low power consumption, low cost and accuracy of 1 / 200 ~ 1 / 500.
Main advantages
Resistance, inductance and capacitance are three kinds of passive components in electronic technology. Capacitive sensor is a kind of sensor which changes the measured change into electrical capacity change. It is actually a capacitor with variable parameters.
Capacitive sensors have the following advantages:
(1) High impedance, low power, low input energy.
(2) A large variation can be obtained, so it has high signal-to-noise ratio and system stability.
(3) The dynamic response is fast, the working frequency can reach several megahertz, thick B contact measurement, the measured object is conductor or semiconductor.
(4) It has simple structure and strong adaptability. It can work in harsh environment such as high and low temperature and strong radiation.
With the development of electronic technology and computer technology, the shortcomings of capacitive sensor, such as easy to be interfered with and easily affected by distributed capacitance, have been overcome. Moreover, capacitive grating displacement sensor and integrated capacitive sensor have been developed. Therefore, they have been widely used in non electrical measurement and automatic measurement, which can measure pressure, displacement, speed, acceleration, a degree, thickness and liquid Parameters such as position, humidity, vibration, content of components, etc. Capacitive sensor has a good development prospect.
Main disadvantages: high output impedance, poor load capacity
Disadvantages 2: nonlinear output characteristics; 3. Parasitic capacitance
Electromagnetic force load cell
It works on the principle of balance between the load on the bearing platform and the electromagnetic force. When the measured object is placed on the load-bearing platform, one end of the lever inclines upward; the photoelectric component detects the inclination signal, which flows into the coil after amplification, and generates electromagnetic force to restore the lever to the equilibrium state. The mass of the measured object can be determined by digital conversion of the current which produces the electromagnetic balance force. The accuracy of electromagnetic force sensor is high, up to 1 / 2000 ~ 1 / 60000, but the weighing range is only between tens of Mg and 10 kg.
Variable pole load cell
When the ferromagnetic element is mechanically deformed under the action of the measured object's gravity, the internal stress will produce and the permeability will change, which will change the induced voltage of the secondary coil around both sides of the ferromagnetic element (magnetic pole). By measuring the change of voltage, the force applied to the magnetic pole can be calculated, and then the mass of the measured object can be determined. The accuracy of magnetic pole change sensor is not high, generally 1 / 100, which is suitable for large tonnage weighing work, weighing range is tens of thousands to tens of thousands of kg.
Vibrating load cell
The natural vibration frequency of the elastic element is directly proportional to the square root of the force. By measuring the change of natural frequency, the force acting on the elastic element can be calculated, and then the mass can be obtained. There are two kinds of vibration sensors: vibrating wire type and tuning fork type. The elastic element of vibrating wire sensor is string wire. When the test object is added to the bearing platform, the intersection point of the V-shaped string wire is pulled downward, and the tension of the left chord increases